100% Quality Control: Hulk Vehicle uses advanced testing equipment and technology to test and monitor every link in every key production stage. After the raw materials arrive, we conduct raw material sampling inspection to ensure that they comply with relevant standards and specifications. During the manufacturing and processing of parts, production quality is strictly controlled to ensure the accuracy and stability of parts. At the same time, during the assembly and assembly stages, multiple rounds of visual inspections and functional tests are conducted, including body appearance, internal accessories installation, electrical systems, etc., to ensure that each component reaches a high quality level.
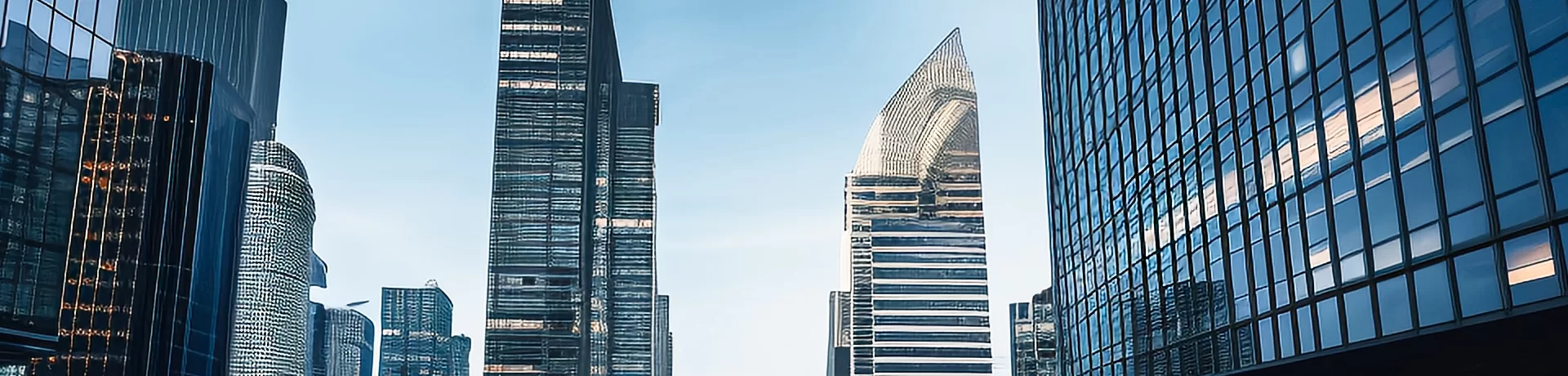
FACTORY SCENE
Hulk Vehicle's factory is a modern, efficient production base located in a vast industrial area. Factory facilities include advanced production lines, equipment and warehousing space, equipped with professional technical teams and management teams. The factory adopts precise production processes and strict quality control standards to ensure product quality and production efficiency.
PRODUCTION & ASSEMBLE
Step 1. Accessories & Material Procurement
Hulk Vehicle has established long-term cooperative relationships with reputable and experienced raw material and accessory suppliers. The purchased raw materials and accessories will undergo strict quality inspection processes, including appearance inspection, dimensional measurement, material composition analysis, etc. At the same time, they will also conduct functional testing to ensure that raw materials and accessories meet design specifications and can meet product performance requirements.

Step 2. Chassis Frame Production
The main beam of chassis frame is integrally stamped and formed from 100X50mm large-section rectangular tubes. Compared with other brands' main beams of 80X40mm rectangular tubes and tailor-welded structures, our frame is stronger and safer. The surface of the frame has been treated with a series of anti-corrosion processes such as pickling, phosphating, electrophoresis, paint dipping, and baking. It has anti-corrosion capabilities both internally and externally, and has a longer service life.

Step 3. Vehicle Overall Assembly
After the vehicle chassis is completed, the overall vehicle assembly begins. The overall assembly process is a precise and complex process, starting from the body structure assembly, where various body parts are combined to ensure that the structure is strong and meets the design requirements. Including but not limited to the installation of drive systems, battery packs, electric control units, wheels, suspension systems, braking systems, etc., to ensure that the vehicle has stable driving performance and safety performance.

Step 4. Testing and Debugging
At all stages of assembly, strict quality control and inspection procedures are implemented throughout. Each component undergoes rigorous inspection to ensure compliance with quality standards and specifications. At the same time, the overall functional testing of the vehicle is also an integral part to ensure that all systems operate normally and meet design requirements. Each vehicle is carefully inspected and performance debugged to ensure the highest level of quality and performance.

Step 5. Packaging and Shipping
After the vehicle production is completed, we will arrange delivery as soon as possible. For small-volume products shipped in LCLs, we use steel frames or plywood for packaging during transportation. For products shipped in full containers, we load them directly into the container, but will fix the four wheels to prevent unnecessary collision damage to vehicles. We provide customers with safe and reliable transportation services to ensure that vehicles arrive at their destination intact during transportation.

Step 5. After-sales Service
Hulk Vehicle provides high-quality after-sales services, including 1-year warranty, maintenance guidance, after-sales support, parts supply, etc., ensuring that customers enjoy free repair or replacement services during the warranty period. Once we receive a call, email or online message from a customer, our professional after-sales team will immediately contact the customer to follow up on the problem and provide timely and effective technical assistance. We offer original parts or certified replacements to ensure vehicle quality and performance.

TEST & DEBUGGING
The quality inspection and safety debugging of Hulk Vehicle is a strict and comprehensive process to ensure that every electric vehicle produced has excellent quality and safety performance, providing customers with a safe and reliable travel tool.
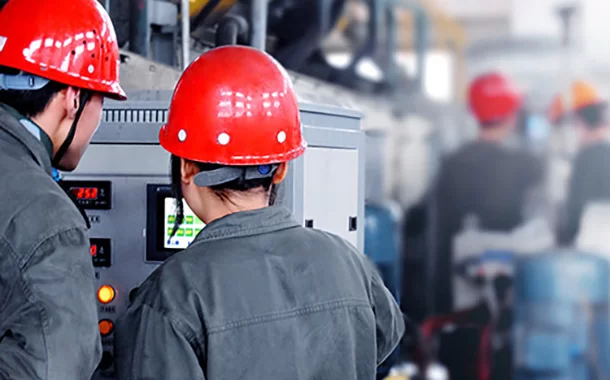
100% Simulation Testing: Safety debugging is one of the key links in the quality inspection process. We conduct comprehensive debugging and optimization of various vehicle safety systems, including braking systems, suspension systems, body stability control systems, etc. Through tests that simulate real road conditions and various emergency situations, we ensure that the vehicle has good stability and controllability during driving. In addition, we also conduct performance tests on vehicles, including tests on acceleration performance, cruising range, charging efficiency, etc., to ensure that vehicle performance meets or exceeds customer expectations.
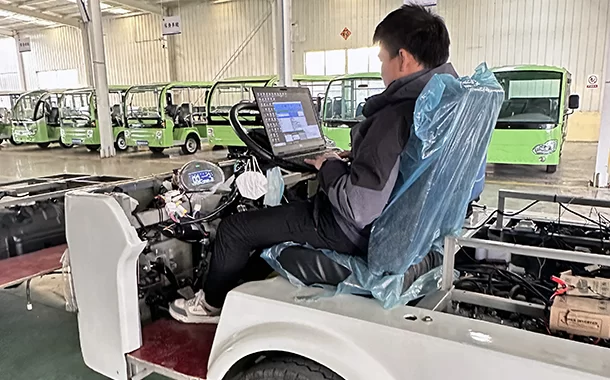
FINISHED PRODUCT
WAREHOUSE